Students shaping industry development from across the globe
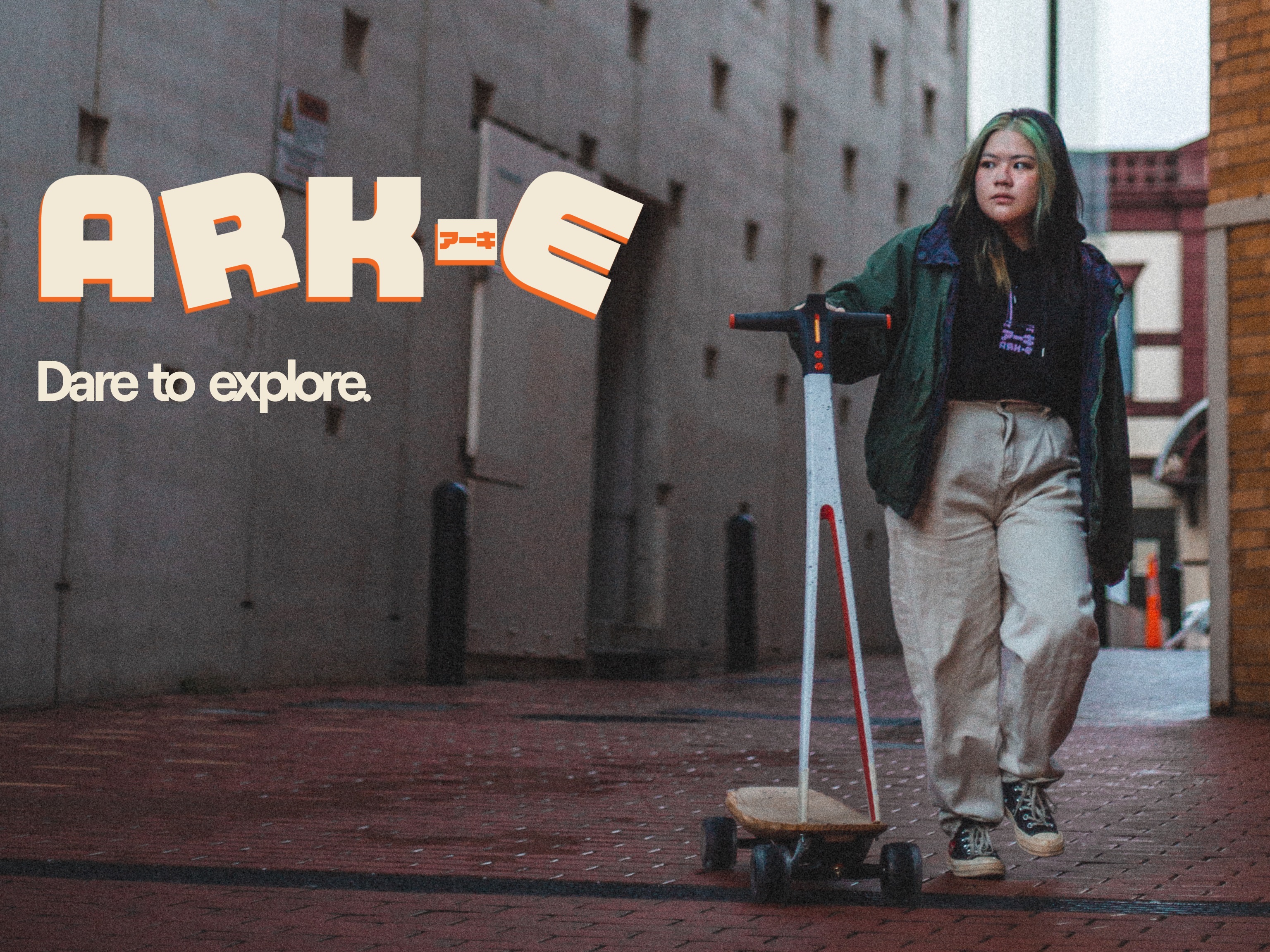
Master of Design student, Ariella Vanya, led the branding and aesthetic considerations for the Ark-e design
In summary
Students from Swinburne and Kyoto Institute of Technology have joined forces to solve a ‘wicked problem’ as part of the SUGAR Network for Design Innovation
The nine-month project put them on the front lines of design development as they worked for industry leader Osaka Gas Chemicals
The outcome was a future-ready design for micro-mobility in Japan, as well as an extensive rationale to help inform the company’s future product development
The ‘fuzzy front end’ of design is where some of the most challenging and impactful creative problem-solving occurs.
SUGAR is a global network of academics, students, and corporate partners, dedicated to giving students experience working at this forward-edge of design.
Students who undertake the nine-month SUGAR program are given experience, knowledge and resources that teach them a real-world, human-centred approach to tackling design challenges.
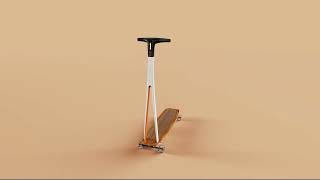
The product design for Ark-e was only the tip of the iceberg, with extensive research and exploration supporting the final outcome
A future-focused solution
The Swinburne Design Factory Melbourne runs the SUGAR program as part of studies in Swinburne’s Master of Design and Design Honours degrees.
Ben Wood and Orin Giesbers, Swinburne Industrial Design Honours students, and Ariella Vanya, Swinburne Master of Design student, joined the project to develop their skills on an international stage, collaborating with students Bisheng Wu, Kagari Miyamoto, Olivia Zhou and Tamaki Hamato from Kyoto Institute of Technology.
“The SUGAR program is about pushing you beyond your comfort zone, to rapidly come to the best solution within a limited time,” Ben said.
“You learn to be comfortable being uncomfortable and to trust your gut, and that's something that can only be done through this sort of trial by fire and having a great support network around you.”
-
Creating the fully functional Ark-e prototype allowed students to develop their technical skills with guidance from Swinburne protolab professionals
-
Creating the fully functional Ark-e prototype allowed students to develop their technical skills with guidance from Swinburne protolab professionals
-
Creating the fully functional Ark-e prototype allowed students to develop their technical skills with guidance from Swinburne protolab professionals
-
Creating the fully functional Ark-e prototype allowed students to develop their technical skills with guidance from Swinburne protolab professionals
-
Creating the fully functional Ark-e prototype allowed students to develop their technical skills with guidance from Swinburne protolab professionals
-
Creating the fully functional Ark-e prototype allowed students to develop their technical skills with guidance from Swinburne protolab professionals
The ‘wicked problem’
During the program, the student team tackled a design problem with no clear or simple solution.
These problems are challenging but have enormous opportunities for innovation and creative problem solving.
For this project, Swinburne students and their counterparts at Kyoto Institute of Technology worked to discover the perfect product to introduce a brand-new sustainable, injection-mouldable material into the market.
The industry client for the project was Japanese company Osaka Gas Chemicals (OGC), who are currently refining a lightweight, high-strength, biodegradable material called Fluorene Cellulose Fibre (FLCF).
Professor at the Swinburne Design Factory Melbourne and SUGAR Network board member, Christine Thong, champions industry-connected projects like this one.
“Industry clients often like to work with students because students can provide fresh perspectives and see new opportunities,” Christine said.
“I saw SUGAR as an opportunity to test everything that I have learned in the past four or five years of my degree in one project with industry partners,” Ben said.
“It’s a big test piece and a big challenge, and it's also very valuable for connections and international experience.”
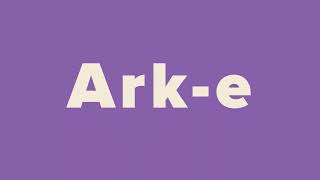
Students shot supporting promotional videos to showcase their designs at the SUGAR Expo
A future-focused solution
Students conducted numerous rounds of detailed research to establish which industry held the most promise for FLCF.
During their months of research and conceptualisation, students uncovered the potential that lightweight, durable and recyclable materials can make micro-mobility more viable, practical and sustainable.
Micro-mobility is still an emerging area in Japan, which makes it the perfect market to introduce a new material over the coming decade.
The team created the design with a future-focus that considered stylistic, social and legal considerations likely to be relevant in the next ten years.
The Swinburne team built a fully functioning prototype in Swinburne’s ProtoLAB, as well as creating a co-designed brand to effectively position the product in the Japanese market.
At the end of the project, they had the chance to present their findings and design to their client and the rest of the SUGAR Network internationally at the SUGAR Expo.
“It's almost unfathomable how much you change and learn from a project like this,” said Ben. “I grew to new levels of resilience and adaptability and worked on my communication skills.”
“It was quite a responsibility and an amazing opportunity that we had and I'm so happy with how it turned out.”
-
Media Enquiries
Related articles
-
- Design
Swinburne alum launches zine celebrating Asian Australian art and identity
Swinburne Graphic Design alum Dan Truong founded HOISZN, a zine publication showcasing Asian Australian artists and their work.
Monday 01 July 2024 -
- Design
Swinburne students shine in lighting design collaboration
Swinburne students collaborated with About Space Lighting, resulting in several student-designed lamps being put into production.
Friday 07 June 2024 -
- University
Swinburne University of Technology partners with Grande Experiences and THE LUME Melbourne for cutting-edge Immersive Media education
Swinburne University of Technology is proud to announce its partnership with Grande Experiences and THE LUME Melbourne, enhancing the future of Immersive Media education.
Thursday 13 June 2024 -
- Design
Yarra Trams feature Women in Trades campaign designed by Swinburne students
School of Design and Architecture students in Swinburne’s Bureau collaborated with Tradeswomen Australia Group to design a tram wrap celebrating women in trades.
Thursday 16 May 2024 -
- Design
- Astronomy
- Technology
- University
Swinburne ‘Rock Muncher’ takes part in Australian Rover Challenge
A multidisciplinary student team from Swinburne University of Technology competed in the 2024 Australian Rover Challenge held in Adelaide, South Australia.
Thursday 11 April 2024