Swinburne to establish world first Industry 4.0 Testlab
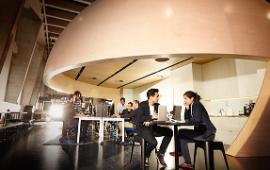
In Summary
- The centrepiece of the Industry 4.0 Testlab is the first industrial scale 3D printing “multilayer” approach to carbon fibre composite manufacture
- Swinburne has partnered with one supplier and three equipment manufacturers to demonstrate the manufacture of commercial parts in an integrated pilot line
Swinburne is establishing the world’s first operational Industry 4.0 Testlab for carbon composite manufacturing as part of its groundbreaking research into digital manufacturing processes.
The centrepiece of Swinburne’s Industry 4.0 Testlab is the world’s first industrial scale 3D printing “multilayer” approach to carbon fibre composite manufacture. The process has been developed by world leading Austrian engineering company Fill, to Swinburne’s specifications in consultation with an industry consortium.
Fill’s unique Multilayer printing technology will be able to produce commercial parts out of carbon fibre at a cheaper cost, with minimal waste and improved production capability.
The Multilayer process represents a digitally enabled step change in technology that will allow Swinburne to build Australia’s first mature Industry 4.0 carbon fibre composite product Testlab.
Transforming the manufacturing process
Industry 4.0 is the digital transformation of manufacturing processes.
Carbon fibre composites are engineered materials offering infinite design flexibility and the opportunity to manufacture smart products. However they are currently difficult to produce in high volumes on a commercial scale due to limitations in manufacturing speed and high labour costs.
Swinburne has partnered with three equipment manufacturers and one supplier to demonstrate the manufacture of actual commercial parts in an integrated pilot line, which in addition to the Multilayer process will include resin dispensing and curing.
This process will be completely digitally controlled from part design and optimisation through to the completed product.
“With our industrial partners, we will create a digital twin of the process and push the boundaries of virtual commissioning,” says Director of Swinburne’s Manufacturing Futures Research Institute, Professor Bronwyn Fox.
Swinburne’s move to implement the Industry 4.0 Testlab comes only months after receiving a record $135 million industrial digitisation grant from engineering giant Siemens to digitise its Factory of the Future and create Australia’s first fully immersed Industry 4.0 facility.
Professor Fox says the Industry 4.0 Testlab will enable Australian manufacturers to have access to cutting edge technology.
“Swinburne, with our partners, will lead the world in providing digital manufacturing solutions to secure Australia’s place in the lucrative intermediate product market.
Linking Australian business to global value chains
“The Advanced Manufacturing Growth Centre (AMGC) has reported that 41 per cent of the global economy is in the intermediate product market and yet Australia participates in less than one per cent of this at present.
“This represents a significant opportunity for Australian SMEs and through our international collaborations Swinburne’s Industry 4.0 Testlab will actively link Australian SMEs into global value chains as we are already doing with our partner Imagine Intelligent Materials.
“Through our partnership with global OEMs we have identified that the real opportunity for Australian industry is not in raw materials but in the high value-add digital design, simulation and manufacture of products.” says Professor Fox.
Professor Fox says global engineering and manufacturering firm, Mulitmatic, is also partnering with Swinburne on the Multilayer process and Industry 4.0 Testlab to help explore opportunities for manufacturing processes that might help in developing new products for the automotive industry at competitive prices.
Swinburne Deputy Vice Chancellor (Research), Professor Aleksandar Subic, says new generation materials such as carbon fibre composites are at the heart of Swinburne’s Industry 4.0 Testlab and Factory of the Future.
“In order to make high value-add products from such materials affordable to manufacture on scale in Australia we are developing technologies and processes that have the potential to disrupt and transform the manufacturing and infrastructure industries,” says Professor Subic.
“The partnership with Fill (Austria) is of particular importance to our strategy as it allows us to introduce a unique form of 3D printing technology for composite products to our lab and fully automate the process.
“In the final stage, we will digitalise the lab through our strategic partnership with Siemens and the $135 Million industrial digitalisation grant awarded to Swinburne at the end of last year.
“This will be the first Industry 4.0 fully operational pilot plant of its kind in the world, offering unique educational and research opportunities to our students, staff and industry partners.”
About Fill
Fill is an international special machinery and plant construction company for various industrial sectors in Gurten in the Innviertel, Upper Austria. Its business activities include the metal, plastic and wood sectors for the automotive, aerospace, wind power, sports and construction industries. The family business founded in 1966 employs around 800 people.