Students show how sustainability is more than recycling
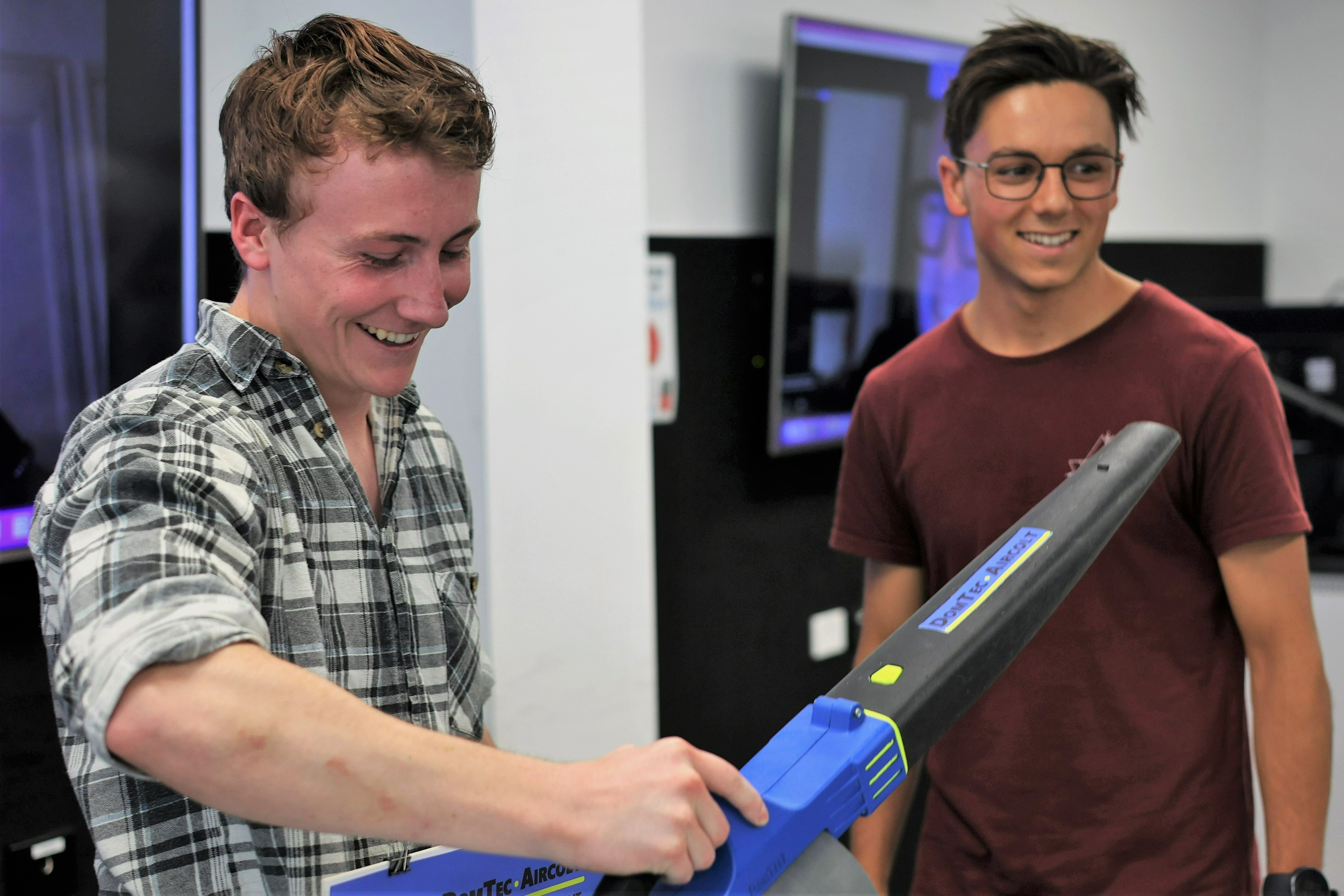
Declan Scott (left) and Thomas Fisher were awarded Best Product Design Engineering Project in the right to repair Showcase
In summary
Product design engineering and industrial design students have embraced a right to repair approach to design and engineer sustainable leaf blowers as part of an industry linked project.
The ‘right to repair’ is the latest sustainability movement sweeping the globe, which advocates for the design of products that can be repaired
Students presented their designs in a showcase that they hope will influence government and industry decision makers
Swinburne students are delivering the next generation of sustainability now through the design of repairable leaf blowers as part of an industry linked project.
A growing sustainability movement that is sweeping the globe, the ‘right to repair’ advocates for the design of easily repairable products, providing a longer lifespan.
It’s also a more effective approach to reducing waste and emissions as these materials stay in use for longer.
-
Joshua McShanag and Thea Davey’s design for hypothetical sub-brand “Ryobi Green” was awarded Best Project for Industrial Design
-
Students also looked at how best to motivate consumers to repair products when they have become accustomed to a disposable mindset
-
Creating a design that comes apart easily not only increases reparability, but also means parts can be more easily be reused when the product does reach the end of its life
-
Industrial designers focused on making their products intuitively repairable
Repairing the environment
Swinburne design lecturer, Kate Bissett-Johnson, has been teaching and researching sustainability for over 20 years and is passionate about passing her knowledge on to her students.
“Right to repair is one of the key movements in sustainability,” Kate said.
“This is the cutting edge. We can't just do what everyone else is doing — design from recycled materials — and that's it.
“When you look at the concept of circular economy, recycling is only a small part of the move towards sustainable product design.
“Repairability requires a whole new way of thinking about how you design your product from the ground up.”
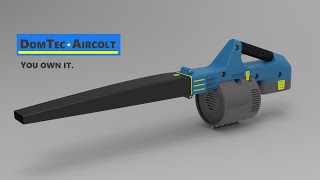
In only 12 weeks, Declan and Thomas created a fully functioning prototype and supporting material, including this kickstarter style video
Training proactive designers and engineers of the future
Students began the project with a tour of a local product recycling company to see the shortcomings and opportunities in the current Australian system.
Declan Scott and Thomas Fisher were awarded Best Product Design Engineering Project.
“Visiting an actual recycling facility made the issue of sustainable design a reality and pushed me to learn how we can improve practices as product design engineers,” Declan said.
Each team also had to go and interview potential users to find out if and how they would repair a product and identify any barriers.
“I think the greatest thing I have learned is how important it is to bring the everyday consumer on board and how intuitive things must be for them,” Joshua McShanag said.
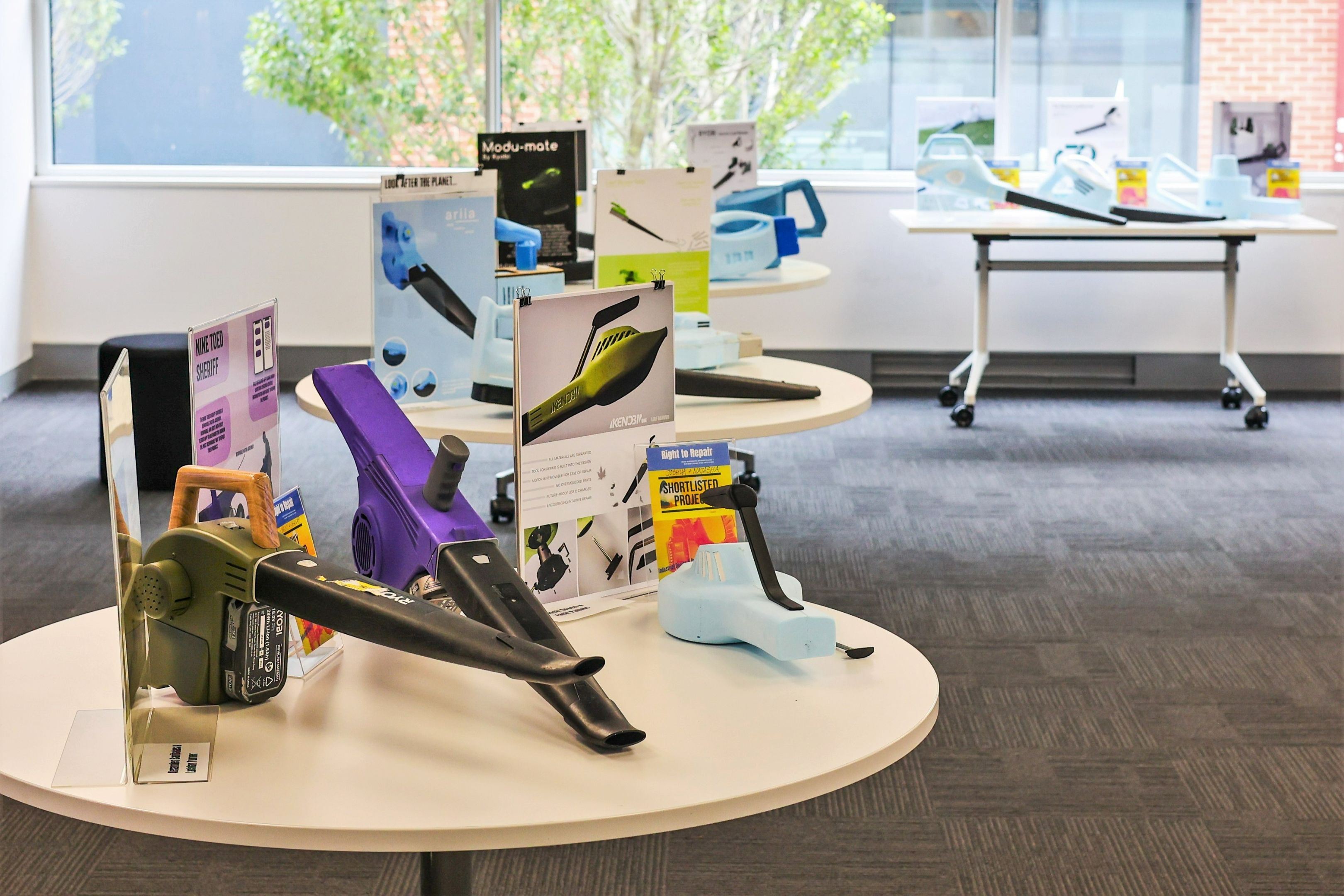
Working prototypes and form studies were made in the Swinburne Protolab, bringing student designs to life
Celebrating achievement
At the end of the project, students presented their designs to a leading industry alum from the Netherlands as part of a showcase.
The industry expert gave students encouragement and feedback and picked the top designs from each of the cohorts.
Each member of the winning project team was gifted a keep cup and a book "Design for Sustainability Survival Guide” to help them continue their journeys as sustainable designers and engineers.
“I now have a strong understanding of my obligations to socially responsible design, and how much impact I’ll be able to have as a future Product Design Engineer,” Thomas Fisher said.
-
Media Enquiries
Related articles
-
- Design
Swinburne alum launches zine celebrating Asian Australian art and identity
Swinburne Graphic Design alum Dan Truong founded HOISZN, a zine publication showcasing Asian Australian artists and their work.
Monday 01 July 2024 -
- Design
Swinburne students shine in lighting design collaboration
Swinburne students collaborated with About Space Lighting, resulting in several student-designed lamps being put into production.
Friday 07 June 2024 -
- University
Swinburne University of Technology partners with Grande Experiences and THE LUME Melbourne for cutting-edge Immersive Media education
Swinburne University of Technology is proud to announce its partnership with Grande Experiences and THE LUME Melbourne, enhancing the future of Immersive Media education.
Thursday 13 June 2024