Timber pavilion design made with low-value timber
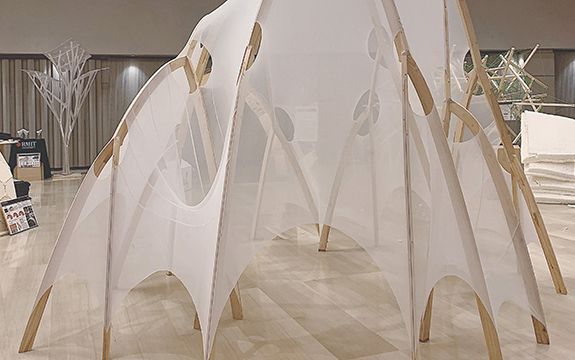
The Suspended Remnants Pavilion in Barcelona. | Image credit: Canhui Chen
In summary
- Computational tool creates funicular geometry with material inventory constraint
- Swinburne collaborates with UniQ, ARC Future Timber Hub and Hyne Timber
- Winning entry in International Association for Shell and Spatial Structures exhibition
Swinburne Lecturer in Architecture, Canhui Chen, and Dean of Design, Professor Jane Burry, have collaborated with the University of Queensland, ARC Future Timber Hub and Hyne Timber to research, design, fabricate and build a funicular timber pavilion structure.
The structure utilises an inventory of low-value, short length timber members and was first presented at the International Association for Shell and Spatial Structures Symposium and an associated competition in Barcelona late last year.
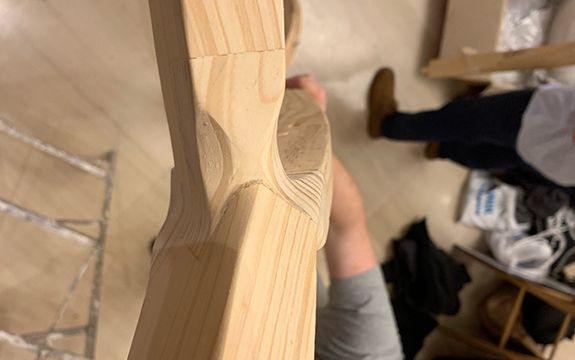
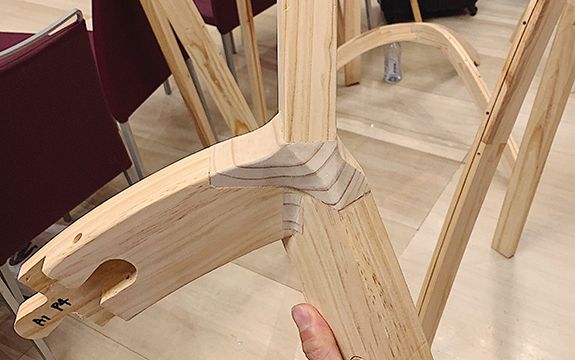
Short unique lengths of timber are assembled to create the structure, image by Canhui Chen
The collaborative research project investigates the development of a bespoke computational tool that combines the generation of funicular geometry with a material inventory constraint. The digital fabrication system is used as a flexible design tool to facilitate exploration of structural form while simultaneously satisfying two rationalising criteria.
The tool maintains a balanced structure derived from funicular geometry; and optimises the use of an inventory of timber members of short unique lengths, typically deemed unusable in the industry, to this geometry. The goal of the design is to achieve material efficiency by creating a structurally rational form with minimal material waste.
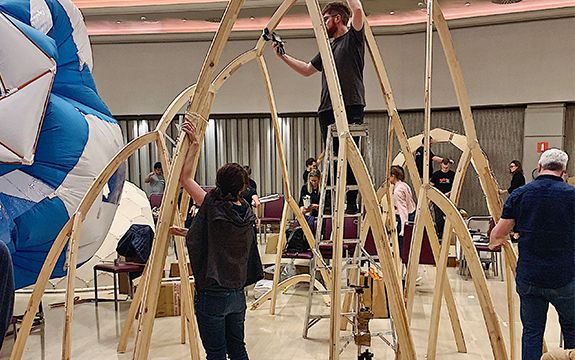

Assembling the pavilion, image by Canhui Chen
The modelling process begins with the digital generation of a funicular ‘base geometry’ of interconnected arches through a “virtual hanging chain simulation” using a particle spring system.
The arches generated within this model are then assessed against the data of an inventory of short length timber via a part assignment heuristic. Based on a minimum curvature tangent differential, and a ‘best fit’ permutation of inventory parts is mapped to the geometry.
The resultant aggregate lengths of the mapped inventory parts are then used to establish precise target length criteria, which are enforced in a second iteration of the dynamic relaxation, where the ‘base geometry’ is automatically adjusted to meet the target lengths, while maintaining its structural equilibrium.
It is proposed that this design and technical workflow could extend beyond the timber industry, to other manufacturing industries that generate offcuts that can be re-purposed, by using this design approach.
“The pavilion structure is constructed using utility-grade sawn timber that is lightweight and has naturally occurring defects. These timber offcuts are typically not certifiable for structural use. When the defects in the timber are removed, they form a unique set of random short structural members. For most commercial framing applications, this variability produces unpredictability and a random inventory of elements which is deemed inconvenient and time-consuming for designers and contractors to work with. However, these short length timbers are well suited to articulated structures seen in inverted funicular geometry,” Canhui Chen explains.
“We developed a computational tool to overcome inconveniences and time inefficiencies of working with random short length timbers by combining a structural form-finding process with an automated part assignment algorithm. This achieves material efficiency through a structurally rational form, while minimising material waste,” says Chen.
“The project was a winning entry in the international competition and exhibition organised by the International Association for Shell and Spatial Structures (IASS) in Barcelona in late 2019,” he says.
“We manufactured the pavilion in Australia using the low-value timber material, transported the pieces to Barcelona in our luggage and built and exhibited it there in October. The pavilion is well travelled. We used only two suitcases and one box to transport it to Barcelona, where it only took just half of a day for four of us to build it. We disassembled and brought the pavilion home to Australia and built it once again for the Future of Prototyping Exhibition in Melbourne,” says Chen.
The Suspended Remnants Pavilion is included in the Future of Prototyping publication.
Swinburne design academics Dr Gregory Quinn and Canhui Chen exhibited their work and research projects at the Future Prototyping Symposium in March.
Media enquiries
-
Media Enquiries
Related articles
-
- Design
Swinburne alum launches zine celebrating Asian Australian art and identity
Swinburne Graphic Design alum Dan Truong founded HOISZN, a zine publication showcasing Asian Australian artists and their work.
Monday 01 July 2024 -
- Design
Swinburne students shine in lighting design collaboration
Swinburne students collaborated with About Space Lighting, resulting in several student-designed lamps being put into production.
Friday 07 June 2024 -
- University
Swinburne University of Technology partners with Grande Experiences and THE LUME Melbourne for cutting-edge Immersive Media education
Swinburne University of Technology is proud to announce its partnership with Grande Experiences and THE LUME Melbourne, enhancing the future of Immersive Media education.
Thursday 13 June 2024 -
- Design
Yarra Trams feature Women in Trades campaign designed by Swinburne students
School of Design and Architecture students in Swinburne’s Bureau collaborated with Tradeswomen Australia Group to design a tram wrap celebrating women in trades.
Thursday 16 May 2024 -
- Design
- Astronomy
- Technology
- University
Swinburne ‘Rock Muncher’ takes part in Australian Rover Challenge
A multidisciplinary student team from Swinburne University of Technology competed in the 2024 Australian Rover Challenge held in Adelaide, South Australia.
Thursday 11 April 2024