Swinburne researcher develops coating to prevent corrosion on ships
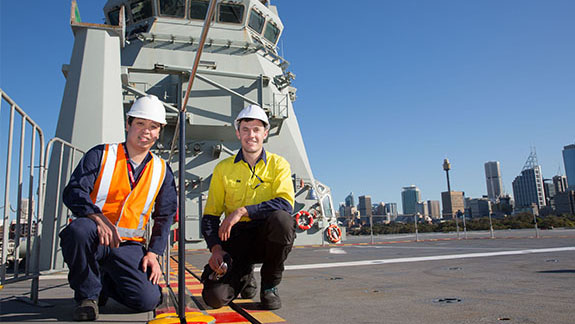
In Summary
- A new corrosion-resistant coating that can halve build-up of algae and barnacles on ships is being trialled on HMAS Canberra
- The project is a collaboration between Swinburne, Defence Materials Technology Centre, MacTaggart Scott Australia, United Surface Technologies and the Defence Science and Technology Group
- Dr Andrew Ang won the 2018 Fresh Science competition in Victoria for his work
Swinburne researchers are collaborating with experts from the Defence Materials Technology Centre, MacTaggart Scott Australia, United Surface Technologies and the Defence Science and Technology Group to advance technology preventing biofouling on ships.
The new corrosion-resistant coating has halved the build-up of algae and barnacles on ship hydraulic components and is now being trialled on HMAS Canberra, one of the Royal Australian Navy landing helicopter dock ships.
Lead researcher on the project, Dr Andrew Ang, collaborated with industry experts to tackle the issue of corrosion and biofouling, where tiny marine plants and animals build up on the surface of things that are constantly in the water, such as ship hulls, anchors and piers.
This build-up can transport pest species to new areas, cause corrosion, damage to critical mechanical components and increase the drag on a ship, causing it to burn more fuel as it sails. These factors combine to impose a massive expense on the shipping industry worldwide.
Applying the coating
“Many scientists around the world are looking for new ways to combat biofouling and corrosion,” Dr Ang says.
“We have developed new materials and used a supersonic combustion flame jet, essentially a flame thrower, to coat hydraulic machinery parts and found these new protective coatings reduce biofouling by roughly 50 per cent compared to current standard coatings.”
A supersonic combustion flame jet (i.e. flame thrower) is used to apply the coating.
The treatment, a single layer of carbide-based coating, is being trialled on parts of ships that require very smooth surfaces usually exposed to harsh operating conditions and as such rapidly degrade from biofouling and corrosion.
The treatment is likely to be too expensive to be used on entire ship hulls, but could impact critically important machinery on a ship that helps provide propulsion or heavy lifting capabilities.
The team tested the protective coating on more than 100 test samples, immersing them in seawater at three field sites around Australia from 2015 to 2017.
The impact of preventing corrosion
Dr Richard Piola, from Defence Science and Technology, says the new surface coatings could make a huge difference to the operational availability of Navy ships, and significantly reduce the cost of maintenance and repairs.
“If the coating can double the length of time a ship can be at sea or available to be deployed—before it needs to be docked and cleaned—it could save costs and also increase operational readiness for the Defence Force,” Dr Piola says.
The team is now testing the protective coating on a prototype system in the field, and have been invited to conduct the trial on HMAS Canberra.
These highly corrosion resistant coatings are new ways to combat biofouling. | DMTC Limited
The Canberra and her sister ship HMAS Adelaide are providing the Australian Defence Force with one of the most capable and sophisticated air-land-sea deployment systems in the world.
Dr Ang won the 2018 Fresh Science competition in Victoria for his work.
Fresh Science
Fresh Science is a national competition run by Science in Public, which helps early-career researchers find and share their stories of discovery.
Fresh Science Victoria is supported by the Royal Society of Victoria, La Trobe University, Monash University, The University of Melbourne, Deakin University, RMIT University, CSIRO and Swinburne University of Technology.
Read the original research paper by Dr Andrew Ang, Matthew Leigh and Associate Professor Scott Wade.