Re-thinking the electronic-waste problem
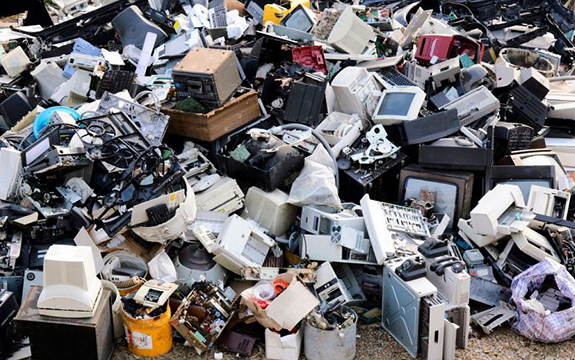
In Summary
- High temperature materials processing expert, Professor Geoff Brooks, discusses Australia’s electronic waste problem
- Professor Brooks is Director of the Joint Research Centre for Advanced Manufacturing in Shandong, China
Our love affair with mobile phones, computers and everything electronic has created a global tsunami of electronic waste. It is estimated that more than 40 million tonnes of e-waste is generated around the world per annum and this is expected to keep growing rapidly for the foreseeable future. There is now widespread appreciation of the electronic waste issue facing consumer societies like Australia.
In Australia, e-waste generation is above 100,000 tonnes and while precise details about where this e-waste ends up are hard to find, the Australian Bureau of Statistics estimated in 2010 that half of the e-waste generated was landfilled, stored or incinerated.
Recent campaigns to raise public awareness about the issue are likely to see the rate of recycling improve, but improved collection of e-waste raises another key issue: How do we safely and effectively process e-waste?
Fortunately, there is significant motivation to process e-waste as it is generally rich in precious metals – gold, silver and palladium - and base metals such as copper, aluminium and iron. Rare earth metals associated with batteries are also very high in economic value. Precious metals make up almost 80 per cent of the value of circuit boards and are many times richer than ores that we mine for these materials so, if separated from casings and other materials, they represent a very attractive ‘urban ore’.
There are also clearly hazardous materials associated with e-waste, such as mercury, lead, arsenic and antimony. Also, in separating the valuable materials from the less valuable (either by heat or using strong chemicals), there will be issues around containing and stabilising waste streams generated from the process.
These problems are solvable (building on the back of improved environmental controls developed for base metal production), but require investment, good regulations and high levels of engineering.
Options for processing e-waste in Australia
Australia has limited capacity to process its own e-waste since the closure of the copper smelting plant in Port Kembla in the 1990s. A re-vamp of the lead smelting plant in Port Pirie should provide a new processing option for e-waste but, as it currently stands, we export most of our e-waste.
As Australia is a signatory to the Basel convention, it is illegal to export e-waste overseas unless the receiving countries have appropriately permitted plants for processing this waste safely and with good environmental protection in place. Recent media investigations suggests that not all our e-waste is going where it should and these problems illustrate the issues with not treating our own waste materials.
This issue could be turned on its head by seeing the e-waste problem as a great opportunity – in particular, seeing e-waste processing as a source of wealth, providing jobs and developing saleable technology.
Australia has outstanding expertise in minerals and metallurgical processing. We are world leaders in many of the technologies that other countries use for e-waste processing.
For example, the Sirosmelt, developed by John Floyd’s team at CSIRO in the 1980s is the furnace technology used by commercially successful e-waste processors in Europe and Asia. A team at Swinburne University of Technology won an international science award in 2013 for their work on optimising that technology and deep expertise about smelting and associated technologies can be found at CSIRO, Swinburne, UNSW, Curtin University and University of Queensland.
Do the economics stack up for e-waste processing industry in Australia?
Currently, most successful e-waste processors in the world are large scale, processing over 200,000 tonnes of waste in large integrated processing plants. In Europe, most of the e-waste collected is treated at an advanced technology plant operated in Antwerp. The operators of this plant have significant research activity around the world on optimising the process.
At the opposite scale, there are also many small operators operating around the world, particularly in the developing world, almost certainly with fewer controls and concern for the environment than with the large integrated process approach.
This approach suggests that Australia could only justify an e-waste processing facility on the basis of treating all the e-waste from Australia, in Australia in one location, which would be logistically very difficult and involve significant transportation and collection costs.
Recently, a techno-economic analysis of e-waste processing technologies carried out at Swinburne found that profitable enterprises could be set up in Australia above the scale of 30,000 tonnes per annum. This analysis implies that Australia could have two or three profitable e-waste processing plants set up in our three biggest population centres. For example, a plant set up in Melbourne could process all the e-waste associated with Victoria and Tasmania, and with improved collection and regulatory support, get processing rates above 30,000 tonnes per annum.
If our society saw this as an opportunity, we could provide the right regulatory environment to encourage investment and try to position Australia as a technological leader in this field, rather than an exporter of a “problem”.
E-waste represents a significant challenge for our society but also represents a great opportunity.
Written by Professor Geoff Brooks, Director of the Joint Research Centre for Advanced Manufacturing in Shandong, China