Swinburne receives grant to lead the charge on Industry 4.0
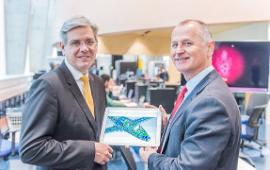
In Summary
- This article originally featured in Swinburne’s Venture magazine
A $135 million industrial grant, awarded to Swinburne by engineering giant Siemens, has placed the university at the forefront of changing technologies in manufacturing.
The grant is the largest industrial fund of its kind awarded in Australia and will allow Swinburne to build on its expertise in fields such as industrial automation, the Internet of Things, new-generation technologies and materials such as graphene and carbon-fibre composites.
Swinburne’s Deputy Vice-Chancellor (Research and Development), Professor Aleksandar Subic, says the nature of industry is changing – and not a moment too soon.
“Western economies can’t continue to compete on labour costs with other parts of the world. That’s why entire automotive assembly manufacturers are moving out of the country,” Professor Subic says. “We’re moving to the creative economy now, the economy of ideas, innovation and high-value-add outcomes.”
In his role as the Chair of Industry 4.0 Testlabs Workstream within the Prime Minister’s Industry 4.0 Taskforce, Professor Subic has spent the past two years developing a national Industry 4.0 framework and translating it into learning and innovation.
Building the future
Industry 4.0 is the latest industrial revolution, building on the change that began in the 19th century with the advent of machine-powered factories and mass production. Early 20th century automotive production lines came next, followed by the blending of automation, robotics and computer controlled systems in the latter half of the 20th century.
Enter Industry 4.0, made possible by the Internet of Things – the embedded connectivity of processes and objects through the internet, based on common standards. Wholesale digitalisation is altering everything in manufacturing, from the development and making of products to post-manufacturing activities such as services and logistics. Big data, analytics and virtual reality models all form vital parts of this holistic digital transformation.
Industry 4.0 also brings radical change to the human element of work. “This level of industrialisation minimises the need for intensive intervention of human labour,” Professor Subic says.
“It allows people to take on the creative side, imagining new products and services and creating new value.”
Swinburne’s Factory of the Future, located in its $100 million Advanced Manufacturing and Design Centre, is a test lab that facilitates and supports education, training and research into advanced manufacturing, in collaboration with industry. There, students and researchers can use design and visualisation tools to develop ideas, produce prototypes and test pilot plants.
“At the moment, our Factory of the Future is a wonderful facility with advanced manufacturing technologies and advanced visualisation, including 3D virtual reality,” Professor Subic says.
Through the grant, Siemens’ Product Lifecycle Management (PLM) and MindSphere platform will assist the factory to be completely digitalised. “Everything will connect in a coherent, seamless digital production system,” Professor Subic says.
“No one does that in this part of the world, using an Industry 4.0 platform of this scale. It will be a completely new paradigm for a completely new type of industry.”
What will this brave new world look like?
“In 12 months you could walk into the Swinburne Factory of the Future and see pilot plants emulating a full Industry 4.0 manufacturing process, end to end – fully automated, fully digitalised, making things seemingly without human intervention. “You’ll see industry partners and experts working alongside our staff and students. You’ll see new and emerging technologies being tested and showcased.
You’ll see students at various levels of education and research, collaborating in multidisciplinary teams.”
Career pioneers
Industry partnerships are already well under way. Siemens is also partnering with Swinburne in a Diploma of Applied Technologies to prepare students for careers in Industry 4.0 domains. The first diploma students enrolled this year.
Student Simon Eves wasn’t after a standard, classroom-based university course to further his career. “In our work placements, we’re applying what we learn at uni to what we’re doing throughout the year and developing our skills,” he says.
Fellow student and former IT consultant, Patrick Stanton says: “They’re using our feedback to adapt the curriculum to be more accurate about what’s needed in the workplace.”
Students are also using cutting-edge technology at Siemens and on campus. Anesu Kanyongo comes to the course with a decade’s experience as a mechanical engineer. “This is a good opportunity to get my mind working again, challenge myself and remain relevant in the industry,” she says.
The work placement aspect of the course is a bonus. “It makes a huge difference in terms of how you apply yourself and see the relevance of what you’re doing. And while you’re doing it, the people around you can see your capabilities and mentor you in the process, instead of waiting for exposure till you graduate.”
Industry partners
Swinburne is working with companies including Asahi, Ford, Multimatic, Siemens, Boeing and Sandvik on projects related to new industry processes, products and materials.
“Together with Siemens, the Australian Industry Group, and industry partners in general, we’re piloting a new model of public-private sector partnerships both in education and research,” Professor Subic says.
In 12 months you could walk into the Swinburne Factory of the Future and see pilot plants emulating a full Industry 4.0 manufacturing process...
Swinburne is also pioneering education in the field and new ways for education and industry to collaborate.
“We have a strategy for Industry 4.0 across the entire life cycle of education, from vocational training all the way to PhD research,” Professor Subic says.
“We want to enable education that is capability driven and industry embedded, rather than being classroom and textbook based.”