Innovative approach to 3D concrete printing recognised
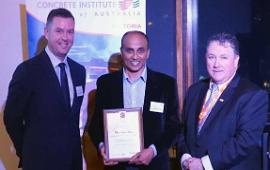
In Summary
- Swinburne researchers receive Concrete Institute of Australia’s Victorian award for Excellence in Technology and Innovation
- 3D printing has potential to change construction, saving huge costs in formwork
Swinburne’s innovative approach to 3D concrete printing using cement and geopolymer binding systems has been recognised at the annual Concrete Institute of Australia (CIA) awards.
The Centre for Sustainable Infrastructure at Swinburne has won the CIA’s Victorian award for Excellence in Technology and Innovation.
Director of the Centre and Professor of Concrete Structures, Professor Jay Sanjayan, says 3D printing has the potential to completely change the way we build with concrete, saving huge costs in formworks and allowing freeform construction.
“At Swinburne we have successfully made the first in-roads into this area by separately using Portland cement and geopolymers as binders in 3D printing machines,” Professor Sanjayan says.
Unlike the conventional approach of casting concrete into a mould, 3D concrete printing combines digital and materials technologies to allow free-form construction without the use of formwork.
In 3D printing the construction is through layer-by-layer addition of material, offering the ability to build components that are otherwise impossible or too expensive to build.
“Engineering and architectural designers are currently constrained to rectilinear designs due to the requirements of formwork systems,” Professor Sanjayan says. “3D Printing will provide the freedom to produce a structural component independent of the shape.
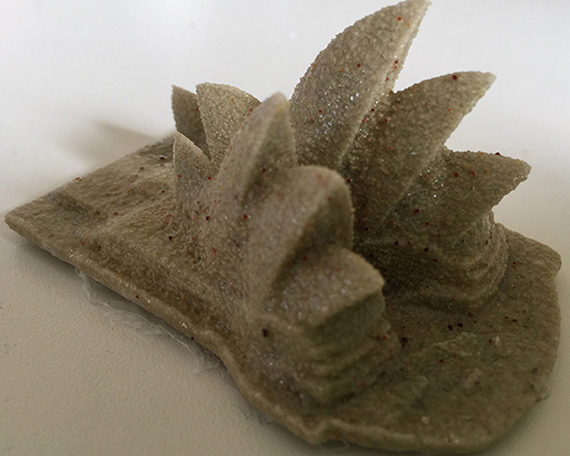
3D printed model of the Sydney Opera House using geopolymer – a cement produced from industrial waste.
“It has the potential to make a major shift in quality control in construction automation, since machines are better at performing repetitive tasks with high accuracy.”
The researchers adapted an existing 3D printing machine to use cement materials combined with fine aggregates to build 3D structures. This prompted the machine makers to invest in making machines for construction applications.
“By choosing the correct particle size distributions and binder deposition methods we have demonstrated how the various technical hurdles can be overcome,” Professor Sanjayan says.
“We have also shown that Geopolymers produced from industrial by-products are a sustainable alternative to the Portland cement system and are more suitable for the 3D printing process as well as how post-processing methods can increase the strengths.”
Dean of Swinburne’s School of Engineering, Professor Emad Gad congratulated Professor Sanjayan and his team for their leadership and innovation in the emerging field of 3D concrete printing.
“Professor Sanjayan’s team has demonstrated the viability of 3D printing powder-based technology for construction applications,” he says.