Swinburne developing life-saving armour to be used on the Bushmaster
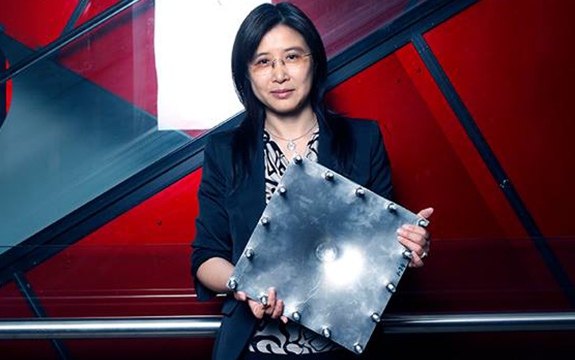
In Summary
- This article originally featured in Swinburne’s Venture magazine.
The people you’re in conflict with are always trying to find a better way to get through your defences
The Bushmaster, an Australian–designed and manufactured infantry mobility vehicle, plays a valuable role protecting our military personnel around the world. Purpose–built to be used in Defence Force operations and commissioned by the Australian Army, the highly protected vehicle has been an important operational asset on a number of deployments, including Iraq and Afghanistan.
The vehicle provides soldiers with blast and ballistic protection from hazards such as improvised explosive devices, in addition to more usual vehicle requirements, such as fuel efficiency and crash survivability.
Engaging research and industry organisations in a collaborative arrangement, the Defence Materials Technology Centre (DMTC) Armour Applications Program is working to develop capabilities for the speedier, more affordable manufacture of these armoured vehicles, offering increased protection and operational performance.
A team from Swinburne is part of the research arm of the project, joining teams from other organisations including the Defence Science and Technology Organisation, Australian Nuclear Science and Technology Organisation, University of Wollongong, The University of Queensland and The University of Melbourne.
These organisations are also collaborating with the industrial supply chain, including steel manufacturer BlueScope Steel, Bisalloy Steel Group Limited – whose thermo–mechanical treatment results in an armour grade steel – and Thales Australia, who manufacture the vehicles.
Ongoing research and development
“No one has died in a Bushmaster protective mobility vehicle,” says James Sandlin, Armour Applications program manager at DMTC. “However the pace at which the threats evolve in modern warfare means that staying one step ahead through maintaining a technology advantage is critical.
“The people you’re in conflict with are always trying to find a better way to get through your defences. So we continue to work with the Bushmaster manufacturer, Thales, to develop technologies that can improve the configuration of that vehicle in response to increasing levels of threat.”
The program is also evaluating concepts for inclusion in a new class of vehicle. The idea being considered could combine the lightness of a High Mobility Multipurpose Wheeled Vehicle with the protection offered by a Bushmaster, resulting in a heavily armoured infantry mobility vehicle that is sufficiently light to be transported by helicopter. The design of such a vehicle is based on using mechanical joints rather than fully seam–welded vehicles.
It is this research that draws on the expertise of Swinburne’s Impact Behaviour of Materials and Structures Group. Led by Dr Dong (Tracy) Ruan, the group is helping to look at how mechanical joins perform in comparison to welded joints under high–impact, high–strain–rate events. Their work involves assessing and comparing these construction techniques and contributing to the advantages and disadvantages of this design approach to further understand the durability of such a vehicle.
In order to use a material we need to understand its mechanical behaviour
World–leading facilities
Facilities at Swinburne’s Hawthorn campus provide one of only a few facilities globally that can test armour strength materials. The comprehensive facilities include a drop tower, split Hopkinson pressure bars, a gas gun and a high–rate INSTRON test machine. This equipment measures the mechanical properties of materials and response of structures under dynamic and impact loads at high speed. The DMTC Armour Applications Program uses most of these facilities.
“In order to use a material we need to understand its mechanical behaviour. In industry a lot of people use computer simulations. But these simulations need the material properties such as the stress–strain curves as inputs,” says Dr Ruan.
Materials under load are often tested in a universal testing machine: a slow, hydraulic press attached to a sensitive set of controls and measures. It conducts compression, tensile, bending and fatigue tests to produce materials stress/strain curves. Swinburne has a MTS 819 machine that can exert a maximum of 250 kilonewtons of force over quasi–static speeds of just 0.05 millimetres per second.
Testing scenarios
Faster events like a car crash – typically 60 kilometres per hour or about 17 metres per second – are more energetic and materials behave quite differently. For these moderate speed tests, Swinburne has secured a high–rate INSTRON machine, the only one in Australia. It can conduct tensile (stretch) tests at up to 25 metres per second and compressive tests at 10 metres per second.
For even higher speed or strain rates, the Impact Behaviour of Materials and Structures group uses split Hopkinson pressure bars. The test sample is sandwiched between input and output bars. A gas–powered striker impacts the input bar, generating a stress wave that compresses the sample, and the propagation of the wave is measured through the sample and bars. There are three sets of split Hopkinson pressure bars of varying sizes, covering a range of temperatures up to 600ºC.
Structures made from a range of materials, such as strong lightweight aluminium honeycombs and sandwich panels can also be assessed. Quasi–static speed tests are undertaken on the MTS and moderate (car crash) speed dynamic tests on the high–rate INSTRON. The drop tower does just that, dropping up to 150 kilograms from a height under controlled conditions to test at speeds around seven metres per second.
“We measure total impact energy absorbed. Energy absorption is a really important property in an impact, if a material can deform and is absorbing a lot of energy it will stop the movement of an impactor and protect the things we want to protect, such as human beings or interior structures,” says Dr Ruan.
Of course, in defence, these structures also need to survive the stresses and strains that occur in a ballistic or blast event. Materials and structures act very differently at these very high impact speeds, failing not as a result of bending or fatigue but from high–speed shockwaves travelling through the material.
Researchers also test for ballistic loads with a nitrogen powered, six–metre–barrelled gas gun. It fires projectiles at up to 600 metres per second with a degree of accuracy and repeatability far better than any rifle. The impact is filmed by a quarter of a million frames per second high–speed camera, which can record the projectile deform on the surface and in some cases even see the shock waves propagating on the surface of the material.
Better designs from data
Together these machines provide critical data input for the design of new vehicles – not just from the shape and structure of the vehicle, but a deep understanding of how those materials might behave in the field. Dr Ruan’s comparisons of mechanical and welded joints are driving vehicle design and materials choice for the DMTC Armour Applications Program industry partners.
Improved material data also helps to build predictive models of how entire armour packages and even vehicles will perform in extreme impact events. Greater confidence in modelling in turn reduces the reliance on iterative real–world testing, saving time and money.
“You really need to know how the materials are going to behave not just as monolithic material but how they’re going to behave in assemblies,” says Sandlin. “That’s where Swinburne has a unique capability”.