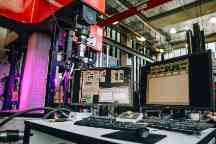
Smart Structures Laboratory
The Smart Structures Laboratory is paving the way for the next generation of structures and construction materials to be thoroughly tested and to provide industry and consumers with the necessary level of confidence in performance and safety.
Swinburne's innovative Smart Structures Laboratory forms part of the Centre for Smart Infrastructure and Digital Construction and conducts research over a broad range of infrastructure-related areas, including large-scale testing of new engineering materials and components.
The laboratory's director, Professor Riadh Al-Mahaidi, is an international leader in the field of bridge engineering, structural systems and structural retrofitting using fibre-reinforced polymer composites. He is joined by several academic staff in the School of Engineering that use the SSL for research and teaching activities.
The only one of its kind in Australia, the $15 million laboratory is located at Hawthorn campus in the architecturally striking Advanced Technologies Centre and features transparent walls, allowing passers-by to watch researchers and scientists at work. The testing facility is available to other Australian universities and to government and industry bodies.
The laboratory's research outcomes are expected to lead to the development of more efficient infrastructure systems and safer buildings, bridges, offshore structures and mining structures. Economic and social benefits should come from more resilient, robust and efficient infrastructure constructed with innovative materials designed to lower costs, improve energy efficiency, and reduce environmental impacts generally.
All this has the potential to lift the international competitiveness of Australian construction and manufacturing industries.
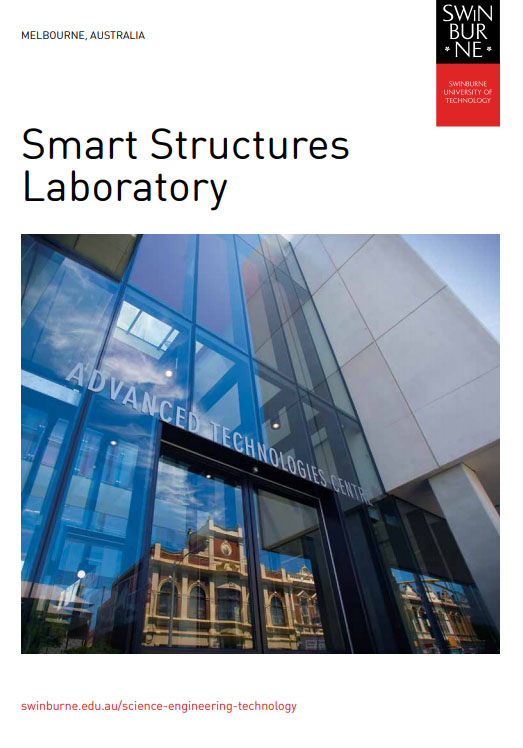
Smart Structures Laboratory brochure
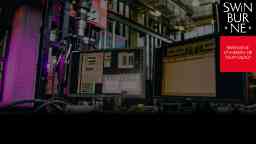
Looking from the outside in
Swinburne's new Advanced Technology Centre brings research that is normally conducted behind closed doors, out to the street. The new glass-walled, street-level, Strong Structures Lab provides a revolutionary space for researchers to test the strength of building materials.
Take a virtual tour of the lab
Our projects
-
Multi-Axis Substructure Testing (MAST) System
View a range of videos showcasing our Multi-Axis Substructure Testing (MAST) System here at Swinburne.
-
Highlighted research projects
View a range of videos that showcase the Smart Structures Laboratory here at Swinburne.
Our areas of research
The Smart Structures Laboratory is involved in an ongoing series of large-scale research and consulting projects. Our advanced equipment and instrumentation allow for a broad range of projects to be undertaken.
Our projects include:
• large-scale 6-DOF hybrid simulation of structures under extreme events
• large-scale 6-DOF quasi-static and cyclic tests of structural components such as beams, wall panels, connections, and underground mine supports
• large-scale pendulum impact testing
• large-scale High-Cycle Fatigue (HCF) testing
• material testing including concrete, steel, timber and composites
• fire testing of panels, cylinders and short columns.
-
“It [the laboratory's hybrid testing facility] minimises error because we are able to test the full-scale component, like a support column, which is far more realistic than a small-scale mode. Of course, this system is not just about earthquakes, but wind loads on buildings, heavy traffic on a bridge, blasts, impacts, ocean waves, materials fatigue… any source of pressure or stress on a structure."
Professor Riadh Al-Mahaidi , Professor of Structural Engineering and Director, Smart Structures Laboratory
Our state-of-the-art equipment
The Smart Structures Laboratory provides equipment for large-scale, quasi-static and cyclic testing of material and structural components, which include:
Multi-Axis Substructure Testing (MAST) system
The laboratory houses Australia's first hybrid testing facility – the Multi-Axis Substructure Testing (MAST) system – cutting-edge technology used to test the integrity of new materials and structures.
The MAST system allows researchers to stress-test structural components and materials to determine a structure or material's capacity to withstand extreme forces (a bridge's capacity to withstand an earthquake, for example).
Read more and watch workshop recordings about our MAST system, combined with the 6-DOF MAST system and others in North America.
MAST hybrid simulation testing
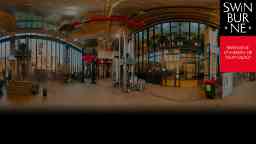
MAST three-dimensional movement
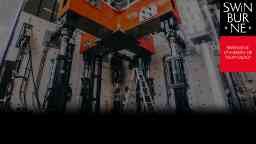
MAST System Designer’s Guide
An outline of the MAST system and its technical specifications.
Download the MAST System Designer’s Guide [PDF, 1MB].
MAST System Resources
The first issue of Up the MAST showcases Swinburne's achievements with the Multi-Axis Substructure Testing facility.
More equipment and facilities
- 5,000 kN Compression static force capacity
- 3,500 kN Tension static force capacity
- Four-column, high-stiffness load frame
- Maximum actuator height: 2.65 m
- Hydraulic lift and locks of upper crosshead
- Actuator in upper crosshead
- Dynacell load cell features compensation for inertial loads caused by heavy fixtures
- Long horizontal three- or four-point bending tests can be reached through structural floor
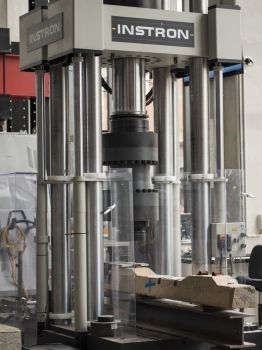
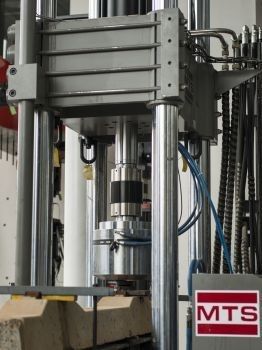
- Static Force Rating: ±1,000 kN
- Dynamic Force Rating: ±750 kN
- Four-column, high-stiffness load frame
- Maximum actuator height: 3.5 m
- Integrated Data Acquisition 16 channels
- MTS Test Suite for conducting these tests:
- Low/High-cycle fatigue
- Fatigue crack growth and fracture toughness
- Crack propagation
- Component strength and durability
- Dynamic characterisation damping
- Tension, Compression, Bending, Shear
- Long Bending tests reacted through floor
Up to ±250 kN static force capacity
Up to ±200 kN dynamic force capacity
Twin-column, high-stiffness, and precision-aligned load frame
Hydraulic Lift and Locks of upper crosshead
Dual servo valve system providing high speed single shot or lower speed conventional static and cyclic testing
Hydraulic grips, fixtures, and accessories
MTS Basic Testware, Multipurpose TestWare and MPE Test Suite software
Integrated Data Acquisition including up to eight strain and eight voltage based; displacement, load or strain transducers.
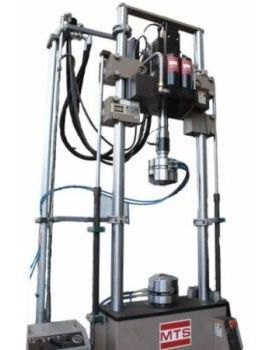
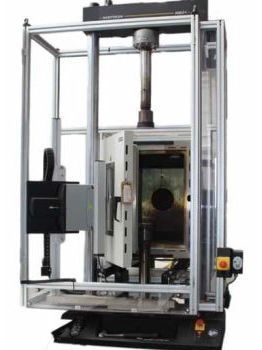
Up to ±100 kN Static Axial force capacity
Up to ±70 kN Dynamic Axial force capacity
Dynacell load cell features compensation for inertial loads caused by grips and fixtures
Maximum Specimen length ~560 mm Compression of ~400 mm Tension
Wide range of grips, fixtures, and accessories
Temperature Controlled chamber capable of holding or cycling between -80 and + 600 Degrees Celsius
Video Extensometer for high precision measurement in Temperature Chamber.
60 kN Maximum
25 MPS Max Velocity
Test volume in chamber: 750 mm x 750 mm x 1000 mm
Data acquisition: High speed acquisition of force and displacement data
Standard tests: Quasi-static compression, tension, bending, etc.
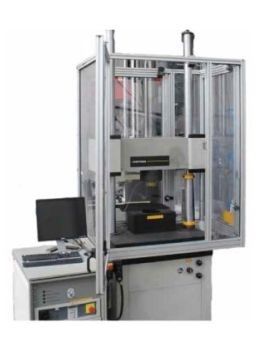
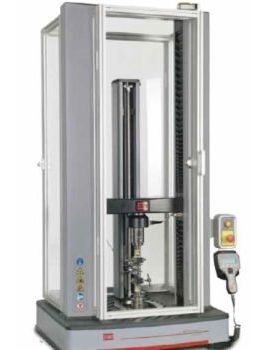
Load frame configuration: two-column, Table top (integrated), Electromechanical ±50 kN Static
Data Acquisition: 2 Axis video extensometer, integrated force and displacement measurement
Typical specimens: small components, reinforced plastics, metals, wire, composites, elastomers, wood products, textiles, biomaterials, paper products, adhesives, foam, consumer products.
- Load frame configuration: two-column, Table top (integrated), Electromechanical ±100 kN Static
- Data Acquisition: 2 Axis video extensometer, integrated force and displacement measurement
- Typical specimens: mid-sized components, reinforced plastics, metals, wire, composites, elastomers, wood products, textiles, biomaterials, paper products, adhesives, foam, consumer products
- Load frame configuration: two-column, Electromechanical ±10 kN Static
- Integrated Data Acquisition with force and displacement measurement
- Typical specimens: small components, reinforced plastics, metals, wire, composites, elastomers, wood products, textiles, biomaterials, paper products, adhesives, foam, consumer products
High torque actuator
5 Environmental chambers with various sizes and capabilities including Co2
Floor shaker, controller, high sensitivity accelerometers and modal analysis software for vibration studies
VSTARS photogrammetry systems including VSTARS-D system capable of measuring at 10Hz n VIC 3D Correlated Solution
Video extensometers
MTS Laser extensometer
1000 Degrees Celsius six zone furnaces
Large number of load cells with various static and dynamic capabilities
Precision LVDTs, LDTs and laser displacement transducers ranging from 2.5mm to 200mm
Multiple National Instruments PXI data acquisitions systems with more than 200 channels
Data Physics data acquisition system for dynamic measurements
Concrete lab
Our research impact and engagement
The Smart Structures Laboratory is significantly contributing to Swinburne’s 2025 strategic plan on achieving research with an emphasis on impact, future-ready learning and innovative enterprises. The lab provides a wide range of internal and external services with more than 60 research and development engineering consulting projects completed in recent years.
A selection of our collaboration partners across various industries (such as construction, automotive, mining and energy) are listed below.
Our partners
-
Würth
-
Fyfe
-
Rondo
-
Grocon
-
k20 Architecture
-
Hickory
-
Timberworks
-
Hilti
-
Embelton
-
Metropolitan Fire Brigade Melbourne
-
NASH
-
Hobson Engineering
-
Dynamic Steel Frame
-
Buildex
-
GCE Consulting Engineers
-
ARUP
-
ITW Construction Systems
-
Geovert
-
ICCONS
-
APEX Building Products
-
Bluescope
-
MiTek
-
Freyssinet
-
Dindas Australia
-
Multiplex
-
Meyer Timber
-
R.J.B. Industries
-
ITW Proline
-
Robovoid
-
Simpson Strong-Tie
-
Sika
-
Knauf
Why partner with us
AEEA High Commendation recipients
For Innovation, Research and Development1
WH Warren Medal recipients
For best paper in the discipline of civil engineering2
Open day exposure
Attract significant attention at Swinburne's Open Day and Student Competition each year3
250+ students
Using the Smart Structures Laboratory across multiple courses4
65+ PhD students
Using the Smart Structures Laboratory for research5
11 ARC-funded experimental programs
Collaborated on since our commissioning in mid-20156
Our people
-
Professor Riadh Al-Mahaidi
Professor of Structural Engineering; Vice President (International Engagement); Director, Smart Structures Laboratory -
Dr Javad Hashemi
Senior Lecturer, Deputy Director, Smart Structures Laboratory
Michael Culton
Laboratory Manager
mculton@swinburne.edu.au
+61 3 9214 8639
Graeme Burnett
Senior Test Engineer
gburnett@swinburne.edu.au
+61 3 9214 8780
Kevin Nievaart
Senior Materials Testing Officer
knievaart@swinburne.edu.au
+61 3 9214 3778
Professor Emad Gad
Dean of School of Engineering
egad@swinburne.edu.au
+61 3 9214 8210
Associate Professor Hing-Ho Tsang
Postgraduate Programme Coordinator (Structural Engineering)
htsang@swinburne.edu.au
+61 3 9214 5009
Dr Robin Kalfat
Senior Lecturer in Civil and Construction Engineering, HDR Advisor
rkalfat@swinburne.edu.au
+61 3 9214 4945
Director, Swinburne’s Centre for Sustainable Infrastructure; Professor of Concrete Structures.
jsanjayan@swinburne.edu.au
+61 3 9214 8034
Explore our news
1 Innovation, Research and Development (High Commendation) for the development of the “Multi-Axis Substructure Testing (MAST) System” by Engineers Australia at the Australian Engineering Excellence Awards (AEEA), (2016)
2 WH Warren Medal by the Board of the College of Civil Engineers of Engineers Australia for the best paper in the discipline of civil engineering “Development and validation of multi-axis substructure testing system for full-scale experiments” (M. J. Hashemi, R. Al-Mahaidi, R. Kalfat, G. Burnett), (2017)
3The SSL also attracts significant attention during the Open Day and Student Competition every year, with live demonstrations using state-of-the-art structural testing equipment.
4250+ undergraduate and post-graduate students at Swinburne use the SSL for demonstrations in several units and courses.
550+ PhD (25+ completed, 25+ current) students at Swinburne use the SSL for research and 15+ PhD students from other organisations.
6 Our research services and engagement since commissioning in mid-2015:
- Five ARC-funded experimental programs for Swinburne University of Technology
- Three ARC-funded experimental programs for Melbourne University
- Two ARC-funded experimental programs for Monash University
- One collaborative experimental program with Auckland University
Contact the Smart Structures Laboratory
If you’re a PhD student, media professional, or an organisation looking to access our facility or partner with us, please get in touch by emailing Professor Riadh Al-Mahaidi at ralmahaidi@swinburne.edu.au or Dr Javad Hashemi at jhashemi@swinburne.edu.au.