Building better resilience through Industry 4.0
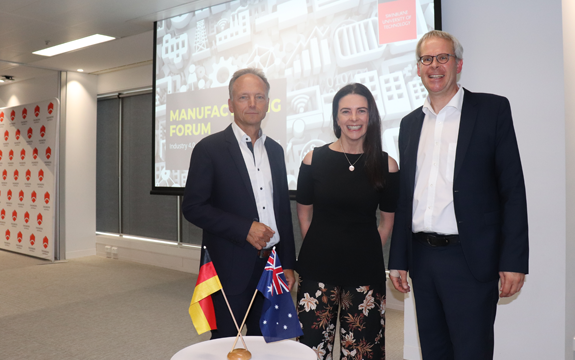
In Summary
- Swinburne’s Manufacturing Research Institute hosted industry leaders and partners at its inaugural Industry 4.0 forum held on 28 February
- Dr Dominik Rohrmus and Professor Frithjof Klasen share how businesses can thrive in this new age
- They also share some insights on what COVID-19 means for Industry 4.0
Back in February, Swinburne’s Manufacturing Futures Research Institute hosted industry leaders and partners at its inaugural forum focused on the latest developments and challenges in the Industry 4.0 space. These partners included Dr Dominik Rohrmus, head of the Manufacturing Systems research group at Siemens Corporate Technology, Germany and Professor Frithjof Klasen from Cologne University of Applied Sciences.
Thriving in Industry 4.0
Industry 4.0 refers to the fourth industrial revolution and includes rapid technological changes like automation and data exchange that are disrupting businesses.
“Industry 4.0 is not a technology you can buy. It is a concept which includes collaboration to integrate operational technology (OT) and information technology (IT),” says Professor Klasen. “Processes in production and logistics become intelligent and integrated, while equipment, products and logistic systems communicate. As such, data and connectivity play an important role,” he adds.
Meanwhile, Professor Klasen says that interoperability between OT and IT is also important to thriving in this space. “Connectivity and interoperability are fundamental prerequisites to share data. Industry 4.0 requires the technical integration of OT and IT systems and convergent networks, down from sensors, edge systems and controllers up to mobile and cloud-based applications,” he says.
Challenges in adjusting to Industry 4.0
However, as Industry 4.0 rapidly ushers in new technologies, this also brings about challenges. For one, small and medium enterprises (SMEs) are struggling to stay competitive in this new age of industry.
Dr Rohrmus explains, “By nature, SMEs do not have departments that deal with digitalisation technology, so they are reliant on global enterprises to support their supply chain. This is where universities like Swinburne play a key role, because you offer resources such as your Factory of the Future and the Advanced Manufacturing Industry 4.0 Hub and make that available as a playground to help these SMEs adapt in a way that they otherwise wouldn’t be able to.”
Swinburne leading the way
Recognising the far-reaching effects of Industry 4.0, Swinburne continues to focus on emerging technologies, industry engagement and flexible learning options to produce career-ready graduates that can adapt and work in this new world.
This sentiment is echoed by Dr Rohrmus and Professor Klasen;
Swinburne’s openness to collaboration has put the university at the forefront of Industry 4.0
Navigating through Industry 4.0 post COVID-19
Much has changed since these insights were shared back in February. The coronavirus (COVID-19) situation has put unprecedented stress on businesses and the global economy and has subsequently impacted Industry 4.0.
“Industry 4.0 and digitisation has taken on a completely new status as a result of COVID-19,” says Professor Klasen. “This pandemic has served as a catalyst for digital transformation in many companies and we expect an unprecedented boost for digital structures in various industries and companies,” he adds. Dr Rohrmus agrees, saying “I am seeing a dramatic increase in interest and awareness towards robotics and autonomous systems as a result of COVID-19. More than ever before, there has been a significant push for research on autonomous systems, security, artificial intelligence (AI).”
Additionally, the COVID-19 situation has brought forward unparalleled disruptions and challenges to the global supply chain. “The COVID-19 situation has made clear how largely dependent many industries are on a single source for raw materials and goods. This is no longer sustainable,” says Professor Klasen. “There needs to be more flexibility and agility in logistics, processes and machinery so we can better deal with similar situations in the future,” he adds.
Dr Rohrmus adds, “while COVID-19 has resulted in massive changes in all regards, I believe it is too early to understand the full extent of these changes. What is certain is that we will come back to a mixed model on the other side.”